Getting The Alcast Company To Work
Getting The Alcast Company To Work
Blog Article
The Single Strategy To Use For Alcast Company
Table of ContentsThe Best Guide To Alcast CompanyAlcast Company for DummiesSome Known Incorrect Statements About Alcast Company Alcast Company - An OverviewThe smart Trick of Alcast Company That Nobody is DiscussingThe Basic Principles Of Alcast Company
The subtle difference depends on the chemical material. Chemical Comparison of Cast Light weight aluminum Alloys Silicon promotes castability by minimizing the alloy's melting temperature and improving fluidness throughout casting. It plays an important role in enabling detailed mold and mildews to be loaded accurately. In addition, silicon adds to the alloy's toughness and put on resistance, making it useful in applications where resilience is vital, such as vehicle parts and engine components.It also boosts the machinability of the alloy, making it less complicated to process right into finished items. In this method, iron adds to the total workability of aluminum alloys. Copper increases electric conductivity, making it advantageous in electrical applications. It also boosts corrosion resistance and includes in the alloy's total strength.
Manganese contributes to the stamina of light weight aluminum alloys and enhances workability (aluminum casting company). It is frequently used in functioned light weight aluminum products like sheets, extrusions, and profiles. The presence of manganese aids in the alloy's formability and resistance to breaking during construction procedures. Magnesium is a light-weight component that supplies stamina and influence resistance to aluminum alloys.
Get This Report on Alcast Company
It permits the manufacturing of lightweight components with exceptional mechanical buildings. Zinc improves the castability of light weight aluminum alloys and aids control the solidification procedure during spreading. It enhances the alloy's toughness and hardness. It is commonly found in applications where elaborate shapes and great details are required, such as attractive spreadings and specific automobile components.
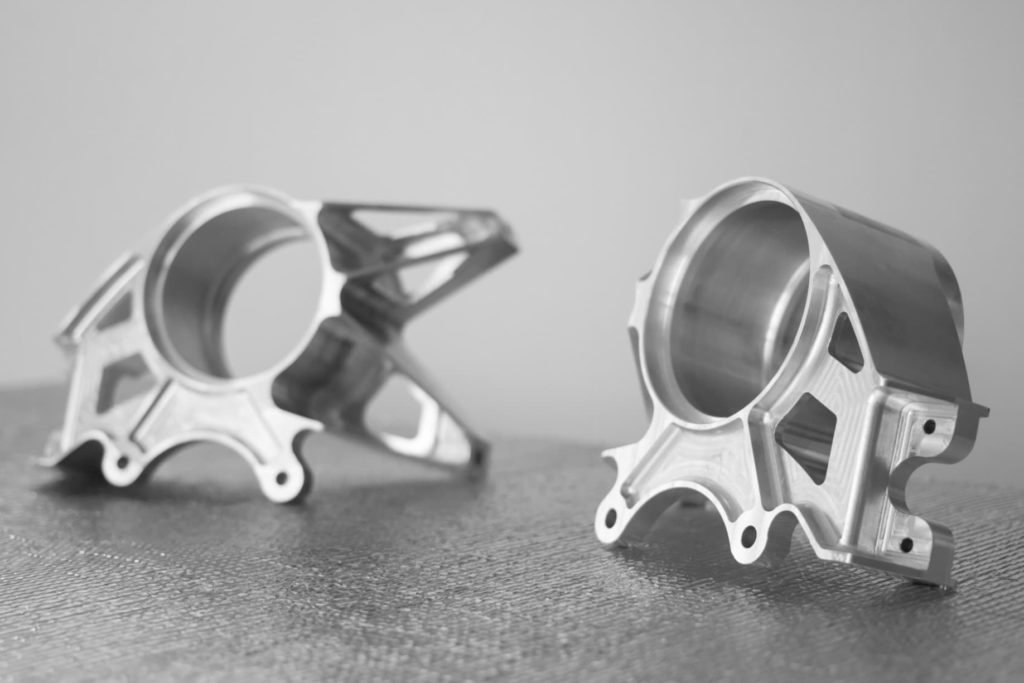
The main thermal conductivity, tensile stamina, yield stamina, and prolongation differ. Select appropriate basic materials according to the efficiency of the target item generated. Among the above alloys, A356 has the highest possible thermal conductivity, and A380 and ADC12 have the most affordable. The tensile limit is the opposite. A360 has the very best return stamina and the highest possible prolongation price.
Our Alcast Company Diaries

In precision casting, 6063 is well-suited for applications where intricate geometries and top quality surface finishes are extremely important. Instances consist of telecommunication units, where the alloy's premium formability permits for smooth and visually pleasing styles while maintaining architectural integrity. Likewise, in the Illumination Solutions market, precision-cast 6063 components create stylish and effective illumination components that require detailed shapes and good thermal performance.
The A360 displays exceptional elongation, making it ideal for facility and thin-walled check my blog parts. In accuracy spreading applications, A360 is fit for industries such as Customer Electronic Devices, Telecommunication, and Power Tools.
The Best Guide To Alcast Company
Its distinct properties make A360 an important choice for precision casting in these markets, enhancing product sturdiness and top quality. Aluminum alloy 380, or A380, is a widely made use of casting alloy with numerous distinct characteristics. It offers excellent castability, making it a suitable choice for precision spreading. A380 exhibits great fluidness when molten, ensuring elaborate and in-depth molds are accurately recreated.
In precision casting, aluminum 413 shines in the Customer Electronic Devices and Power Tools markets. This alloy's exceptional corrosion resistance makes it an exceptional choice for exterior applications, making sure long-lasting, long lasting items in the mentioned markets.
Things about Alcast Company
The aluminum alloy you choose will substantially affect both the spreading process and the homes of the last product. Due to the fact that of this, you must make your decision carefully and take an enlightened strategy.
Determining the most appropriate light weight aluminum alloy for your application will certainly mean considering a large selection of features. The initial group addresses alloy qualities that impact the production process.
Our Alcast Company PDFs
The alloy you select for die spreading directly influences numerous aspects of the casting procedure, like just how very easy the alloy is to deal with and if it is prone to casting defects. Warm cracking, additionally known as solidification fracturing, is a normal die spreading defect for aluminum alloys that can result in inner or surface-level rips or cracks.
Specific aluminum alloys are extra prone to hot fracturing than others, and your choice ought to consider this. It can damage both the cast and the die, so you must look for alloys with high anti-soldering properties.
Rust resistance, which is currently a noteworthy feature of light weight aluminum, can vary significantly from alloy to alloy and is a necessary particular to take into consideration relying on the ecological problems your product will be exposed to (aluminum casting manufacturer). Use resistance is another building commonly sought in aluminum items and can differentiate some alloys
Report this page